Pražce ze Štětí
Firma KŠ PREFA vybudovala novou halu, jejíž dominantou je linka na betonové železniční pražce. Nejnovější akvizici závodu ve Štětí, jehož provoz se úzce týká i spolupráce s Holcim Česko, představili ředitel závodu Zdeněk Zdvihal a technolog Jan Marek.
Co si slibujete od vybudování nové linky?
Zdeněk Zdvihal: Závod KŠ PREFA ve Štětí se věnuje většinou přípravě zakázek „na klíč“ – atypických betonových výrobků podle konkrétních požadavků zákazníka, jako jsou třeba části lávek z vysokopevnostního betonu. Díky nové automatizované lince na železniční pražce teď máme možnost vytvářet produkt, jenž lze vyrábět průběžně tzv. „na sklad“.
Kdy došlo k rozhodnutí investovat právě do linky na betonové pražce?
Zdeněk Zdvihal: Rozhodnutí vzniklo v době, kdy společnost Skanska, její divize zabývající se dopravními stavbami, byla zavázána spolupracovat s českými dodavateli. Proto padl návrh začít vyrábět pražce právě zde. Ve chvíli, kdy Prefu převzal současný majitel, bylo rozhodnuto v tomto plánu pokračovat. Záměr se ale povedlo naplnit dnes.
Technickou dokumentaci k výrobku jste vyvíjeli ve vlastní režii?
Nebo se jedná o standardizovaný pražec?
Zdeněk Zdvihal: Dokumentaci jsme si vyvinuli sami ve spolupráci s ČVUT.
Jan Marek: Přesto – platí pravidlo, že pražec musí podléhat určité standardizaci, například existují požadavky, aby byl tzv. interoperabilní. To je požadavek, aby se dalo jezdit v celé Evropě po typizovaných pražcích ve stejném rozchodu, aby mohly vlaky přejíždět z Portugalska až do Ruska.
Je možné, že pražce mají různý technický design, různý je i použitý materiál, ale vnější geometrie pražce i koleje musí být dodržena.
Můžete specifikovat použitý beton?
Jan Marek: Jedná se o beton jedné z vyšších tříd pevnosti, ale standardní kvality. Ještě doplním, že technických řešení, jak vyrábět pražce, je více. Výběr technologie závisí také na tom, jak velkou výrobní kapacitu vlastně potřebujete. My jsme celkovou kapacitu linky přizpůsobovali požadavkům trhu v České republice, protože se stále jedná o betonový výrobek a nemá smysl ho vozit stovky nebo tisíce kilometrů daleko.
Při výběru dodavatele jste vybírali z několika možných rem. Na základě jakých kritérií bylo rozhodnuto o vítězi?
Jan Marek: Dodavatele jsme hledali v rámci otevřeného výběrového řízení. Prošli jsme si několik linek v rámci Evropy, například ve Švédsku, ve Švýcarsku, v Německu, v Belgii, v Itálii. Z nich jsme si vybrali nejlepší technické řešení. Sestavili jsme podmínky tak, aby budoucí linka splňovala všechna naše specifika. Pak jsme řešili otázku, který z dodavatelů se jim bude schopen přizpůsobit.
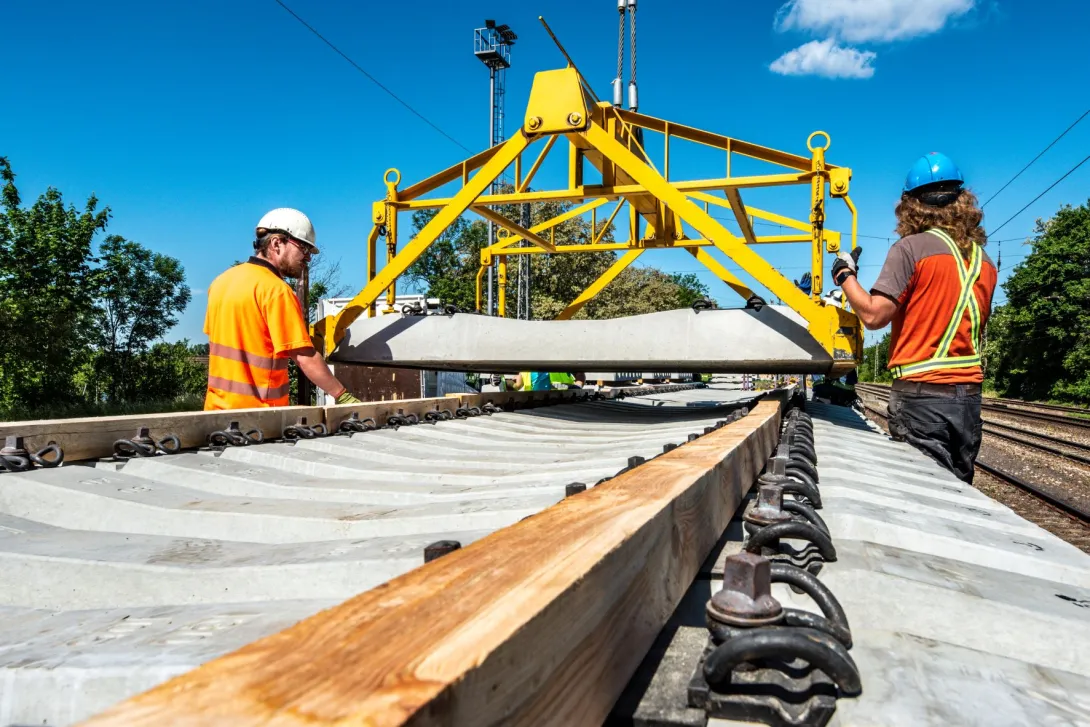
V čem se odlišovaly nabídky jiných dodavatelů?
Jan Marek: V první řadě nás zajímala co nejmenší pracnost, dále kontinuita výroby, a hlavně co nejnižší nároky na personální obsazenost.
Kolik lidí nakonec doopravdy pracuje na lince?
Zdeněk Zdvihal: Aktuálně ji rozbíháme, tak uvidíme, jak se nám povede obsazenost optimalizovat. Ale v ideálním stavu by ji mělo obsloužit osm až deset lidí.
Dá se říct, jaké zvýšení obratu očekáváte?
Jan Marek: V uplynulém roce jsme měli obrat zhruba pět set milionů. S pražci by se to mělo navýšit zhruba o dvě stě milionů. Pokud jde o závod Štětí, ten bychom měli při plně vytížené lince zvednout o maximálně padesát procent.
Můžete popsat vámi zvolené technické řešení?
Jan Marek: Na naší lince se pražce vyrábějí a přepínají na dlouhé dráze v řadách za sebou. Jedna řada je dlouhá zhruba 85 m, takže se přepíná zhruba 90 m délky.
Celá délka se najednou zabetonuje a po vyzrání betonu se pražce rozřezávají na jednotlivé kusy. Naše linka má poměrně velkou míru automatizace a robotizace, to vždy odpovídá finančním možnostem a se smysluplnou návratností: máme automatizovanou dopravu betonu z betonárny do haly, máme automatizovanou pilu, která pražce řeže. Máme i nadstandardní způsob sledování geometrie: zařízení, které s vysokou přesností skenuje povrch výrobků. Nesmíme zapomenout ani na robotické skladování v meziskladu, kde pražce jeden den zrají a na robotizovanou skládku.
Velmi dobře a progresivně máte vyřešeno hospodaření s vodou.
Zdeněk Zdvihal: Co se týče samotného řezu pražce, zachytáváme vodu, která je potřeba
k chlazení, do sedimentačních nádrží, z nichž vodu přesouváme přes kalolis, kde odstřeďujeme vzniklý prach. Vodu takto čistíme a potom ji přečerpáváme zpět do nádrží a vracíme ji do oběhu celého procesu. Díky tomu jsme při hospodaření s vodou víceméně soběstační.
Vaše dosavadní výrobní hala vznikla roku 2008. Jaký je technologický rozdíl mezi oběma budovami?
Jan Marek: V našem portfoliu výrobků máme tzv. „hala systém“, jenž se skládá ze stěnových zateplených nosných prvků a betonových střech, jež jsme použili na stavbu nové haly. Maximální rozpětí střechy tohoto systému může být až 32,6 m.
Díky tomu, že je střecha i celý plášť budovy dobře izolovaný, šetříme spoustu energie jak v létě, tak v zimě. Snižujeme požadavek na vytápění a v létě nemusíme chladit.
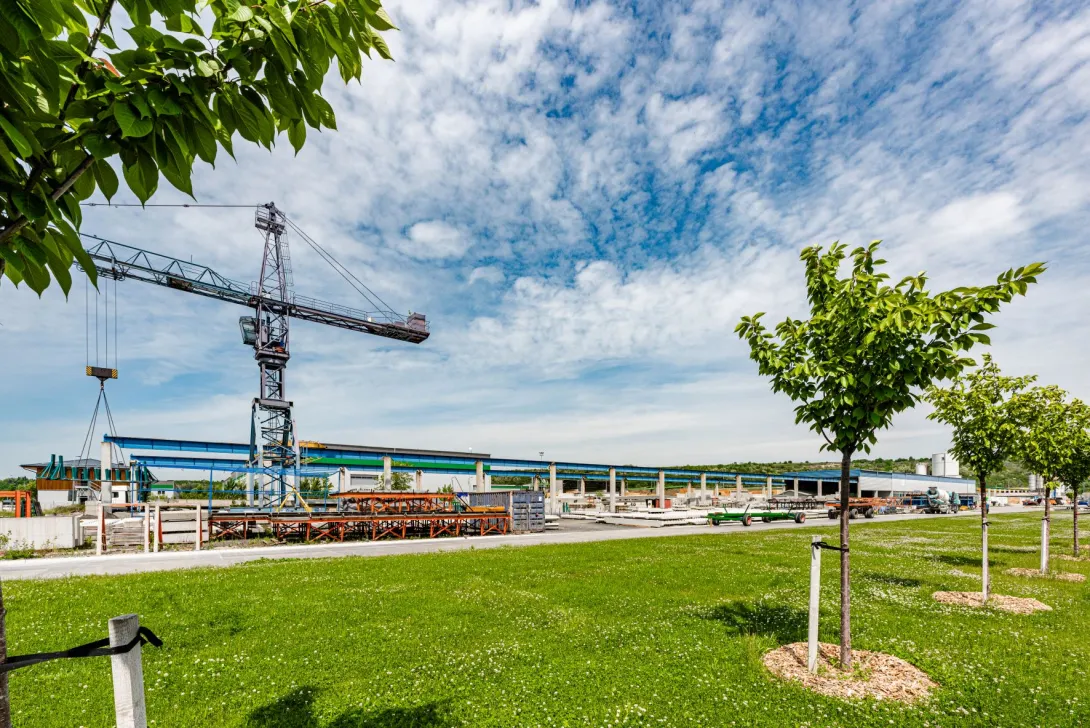
Je hala vytápěná?
Zdeněk Zdvihal: Hala je vytápěná plynem a o chlazení neuvažujeme.
Jan Marek: Pro výrobu betonových prefabrikátů je skutečně vhodné vyrovnané klima,
v halách tedy nemůžeme mít teploty, které by výrazně kolísaly. Proto jsme víc investovali do budovy, aby měla stabilnější klima. Technologická linka má v sobě navíc zabudován systém předehřívání a ohřívání forem, který se používá v Holandsku, Švédsku či v Německu. U nás zatím není používání takové technologie ohřevu nutné, ale my chceme být do budoucna připraveni.
Na co konkrétně?
Jan Marek: Předpokládám, že v budoucnosti se současný typ cementu již nebude
v prefabrikaci používat. Budou se používat nějaké směsné cementy, které nemají tak rychlý nástup pevnosti. Pak bude potřeba beton prohřívat, na což jsme díky nové lince již připraveni. Můžeme tak mnohem snáze reagovat na požadavky na snižování emisí CO2 i na změnu receptury, ale pořád dodržovat stejný výrobní cyklus.
Jaká je kapacita nové linky?
Zdeněk Zdvihal: Jsme schopni vyrábět téměř čtyři sta pražců denně, je to tedy téměř sto tisíc pražců za rok. A díky velké skladovací kapacitě jsme připraveni uskladnit tři čtvrtě roku až rok naší produkce.
Kam míříte s vašimi výrobky?
Jan Marek: V tuto chvíli je to Správa železnic, která je aktuálně náš ideální zákazník. Můžeme výrobu ještě rozšířit o další typy pražců nebo můžeme i tyto pražce připravit na jiný typ upevnění. Je to spíš otázka ekonomická, jestli nám přijde tak velká poptávka, která by investici do úpravy zaplatila.
Vaše pražce jsou určeny pro běžnou železniční síť, zatím ale ne pro vysokorychlostní tratě.
Jak moc náročná by byla úprava linky, třeba právě pro pražce jiného typu?
Jan Marek: Většina linky při úpravách zůstane stejná, protože rozchod kolejí bude stejný i délka pražce. Technicky je linka připravená. U nás by změna sortimentu znamenala zejména úpravu forem, ale ostatní součásti zůstanou stejné a velká většina technologií je stále použitelná.
Aktuálně připravujete dodávku několika tisíc pražců na zkušební úsek. Už víte, kde se bude jezdit po vašich pražcích?
Zdeněk Zdvihal: To zatím nevíme. Ale už dnes se po našich pražcích jezdí na prvním zkušebním úseku v Nymburce, díky němuž jsme dostali certifikaci.
Jan Marek: Jsou tam instalované od listopadu roku 2017.
Trať je hodně rušná, několik prvních pražců na začátku úseku je tak extrémně zatíženo, že se předpokládalo, že se poruší. Ale za čtyři roky se to ještě nestalo. Celková očekávaná životnost je minimálně třicet let.
Náš rozhovor je otištěn v časopise Journal.
Jak hodnotíte spolupráci s naší společností?
Zdeněk Zdvihal: Z nedávné minulosti mohu připomenout spolupráci u výroby transport betonu při výstavbě pily v sousedství našeho závodu. Měli jsme před sebou úkol zhruba v osmi měsících umíchat 75 000 m3 betonu, což předpokládalo koordinaci navážení cementu.
Myslím si, že akce byla úspěšná, i generální dodavatel – sdružení firem Strabag a Metrostav byl s dodávkami spokojen. Nejen proto považuji spolupráci s Holcim Česko za velmi dobrou.
Převzato z LC Journalu 1/2021